How to Reduce Workplace Injury with Machine Guarding
What Is Machine Guarding?
Depending on the piece of equipment, moving machine parts can cause a variety of severe workplace injuries, including lacerations, burns, crushing, amputation, and even death. According to the Occupational, Safety, and Health Administration (OSHA), workers who operate and maintain machinery suffer approximately 18,000 amputations, lacerations, crushing injuries, abrasions, and more than 800 deaths yearly. Machine guarding is essential for protecting workers from these preventable injuries.
Machine guarding is a measure used to prevent body parts and unwanted objects from coming into contact with moving parts of machinery. The primary goal of machine guarding is to protect the operator and other employees in the work area from hazards created during the machine’s operation. It is the first line of defense to protect workers from injuries that could occur when the machine is being used.
Types of Machine Guarding
The four main types of machine guarding are fixed, interlocked, adjustable, and self-adjusting.
Fixed machine guards are permanently attached to the machine and can’t be moved while the equipment is in use. These guards are commonly used to enclose hazards that the operator doesn’t need to interact with, such as power transmission. Some examples of fixed guards include gates, fences, barriers, or blade covers.
Interlocked machine guards are built to protect the operator from the moving parts of the machine and automatically disengage the power when the guard is opened or removed.
Adjustable and self-adjusting machine guards adjust to the size of the material. Adjustable guards must be manually adjusted and locked into place.
Determining Machine Risks
To determine whether equipment requires machine guarding, an experienced EHS professional should audit the workplace and assess all equipment for potential risks. An assessment of all moving parts that could result in workers being struck or crushed should be noted.
The EHS professional will oftentimes observe workers operating equipment during their assessment. Machines that have not been inspected in a long period of time should be examined for any signs of damage that could indicate they are not safe to operate. Equipment should also be inspected on a regular basis to see whether it needs maintenance or should be pulled out of the workplace.
Train Workers on Machine Guarding and Recognizing Hazards
Workplaces with machine guards should make sure workers understand the importance of these safety devices, as well as how they work. They should also know to alert managers of any problems with the guards or the machines themselves to address the issue quickly and safely.
Need Help Assessing Hazards? How Walden Can Assist You
Walden’s EHS team has the expertise to help you build a best-in-class safety culture at your organization. Visit our EHS page to explore all of the safety services that we offer, and give us a call at 516-588-6859 to speak with an experienced EHS specialist today.
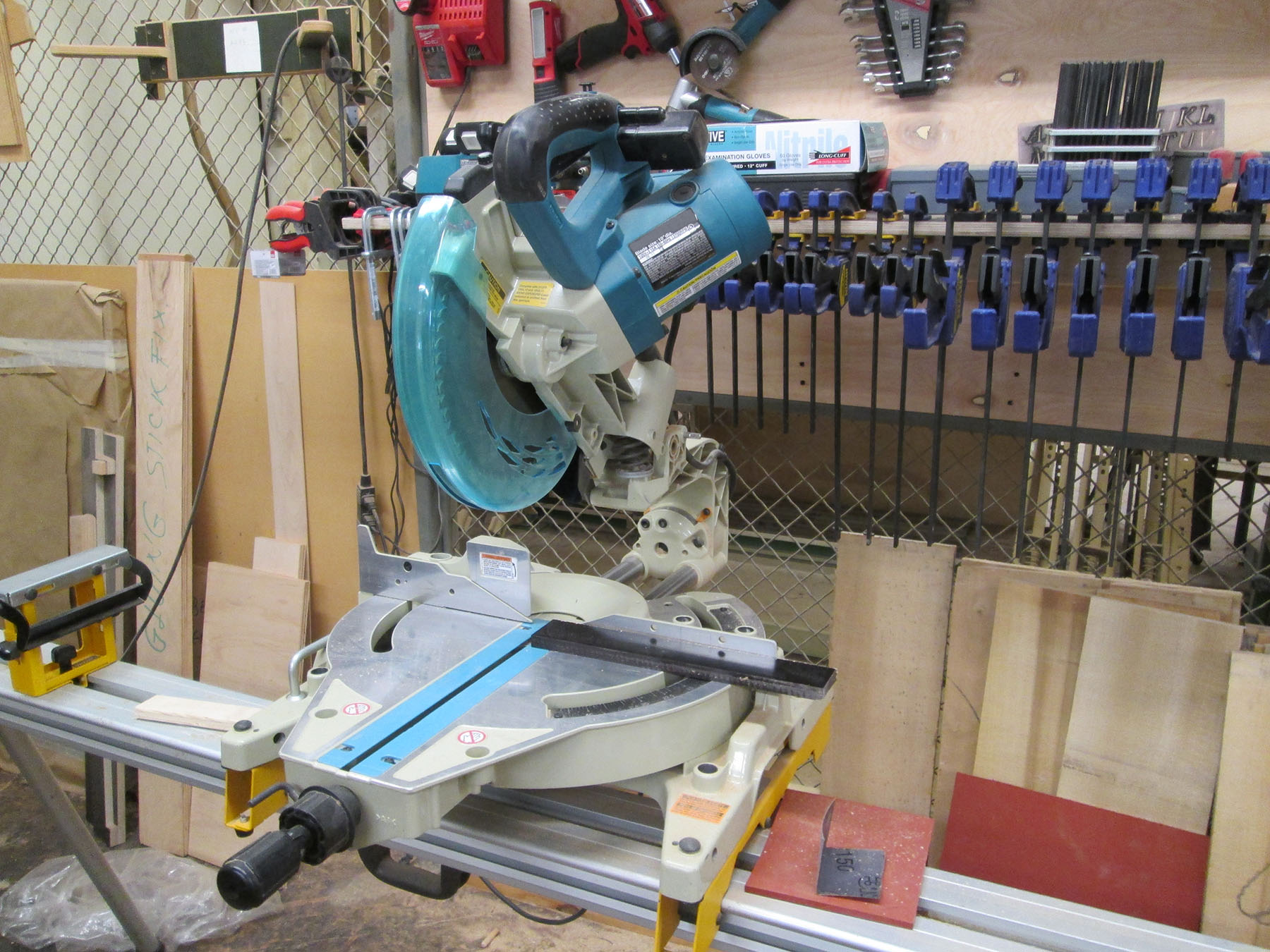
Read more about Walden’s EHS consulting services here and the importance of facility audits here. Contact us at 516-588-6859 to connect with our EHS team!