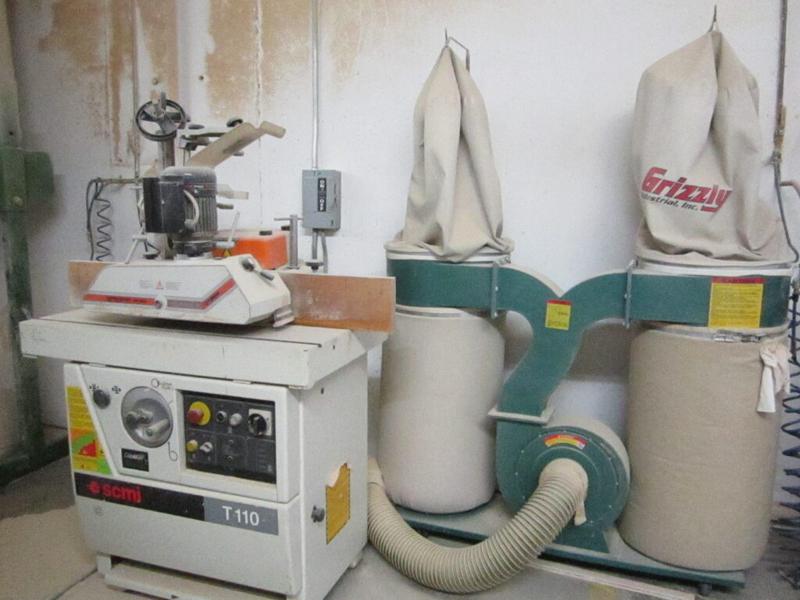
Once a company recognizes that it produces potentially hazardous emissions, it should create an action plan to mitigate any risks and negative impacts. Fortunately, OSHA lays out a clear framework of controls to manage workplace hazards, enabling companies to create a pathway toward a safe work environment.
1. Eliminate the Source
The preferred, and by far most effective, course of action is to eliminate the hazard at the source before a problem can ever occur. OSHA offers an example of how this works: A manufacturer of plastic compounds used lead compounds as heat stabilizers in formulating certain wire and cable products. As state laws changed and end-user demand increased, the company worked with partners in its supply chain to investigate less toxic alternatives than lead and switched to an option that could achieve the same high-quality product performance.
2. Install Engineering Controls
There are, of course, many cases where it’s simply not feasible to replace one chemical or material with another. In this case, the next preferred method of controlling a hazard is to modify the facility by utilizing engineering controls, such as ventilation or fume hoods.
Engineering controls either reduce the generation of a contaminant or limit the amount of a contaminant in the air by exhausting the contaminant and/or cleaning the air. While we will discuss this approach in greater depth in the next chapter, it is important to know that effective engineering controls should be monitored regularly to ensure they remain effective over time and in the face of any change.
3. Apply Administrative and Work Practice Controls
An administrative control limits workers’ exposure to hazardous materials by reducing the amount of time workers spend exposed to a contaminant. This might mean restricting access to a work area or using a work-rest or job rotation schedule that limits the length of time a worker is exposed to a hazardous substance.
For example, OSHA’s PEL for lead is 50 micrograms per cubic meter of air on average over an 8-hour period. So, in a workplace that may exceed this limit, the employer may assign a worker to that environment for four hours and another employee for the other four hours each day, thereby reducing the exposure of each worker on an eight-hour basis to below that PEL.
Because the hazard is not actually eliminated in these instances, these control measures can have some limitations. For example, administrative controls can be difficult to implement because they depend on workers’ compliance. These solutions work best in conjunction with engineering controls and other solutions.
4. Require Personal Protective Equipment
Unlike the three prevention measures listed above, the use of personal protective equipment (PPE) is a protection control. While prevention measures focus on eliminating or reducing the probability that a hazardous condition will occur, PPE instead reduces the magnitude of the hazard. Some OSHA standards set mandatory requirements for PPE such as respirators alongside other types of controls.
As with administrative and work practice controls, PPE requires action from employees, so it can be difficult to ensure compliance. Although PPE may seem like a quick and easy way to solve a problem, it may require more frequent training and reminders to ensure the equipment is being used appropriately and consistently. In addition, employers may find that employees’ overall safety and working conditions might actually be reduced as they are required to wear more layers of PPE, so it is important to alleviate as many hazards as possible upfront.
A Broad Problem-Solving Approach
For many employers, a multi-pronged approach is the most effective way to limit the potential impact of hazardous emissions on workers. For example, as many manufacturing operations will have more than one hazard in the environment, it is important to consider a broad approach that reduces all potential hazards to employees.
Click here to download our full Air Quality Guide: Controlling the Air Quality in Your Facility: What You Need to Know About Your Regulatory Requirements and Options for Compliance.