Hearing Conservation
Did you know that hearing loss from noise is 100% preventable?
Hazardous noise exposures exist outside of the workplace, as well as on the job. OSHA requires employers to implement a hearing conservation program when noise exposure is at or above 85 A-weighted decibels (dBA) for an eight-hour shift or more. Hearing conservation programs strive to:
- Prevent initial occupational hearing loss
- Maintain and protect remaining hearing
- Provide workers with the knowledge and hearing protection devices that they need to stay safe
Under OSHA’s Noise Standard, employers must reduce occupational noise exposure through engineering controls, administrative controls, or hearing protection devices. Noise levels are most likely hazardous if a person must raise their voice to speak with someone only an arm’s length away.
To ensure that your controls are effectively protecting your employees from workplace noise exposures, you must perform annual audiometric testing as part of your hearing conservation program.
Have you had an industrial hygiene study done? Did it include noise exposure?
Noise-induced hearing loss can be temporary or permanent. Temporary hearing loss results from short-term exposures to noise, with normal hearing returning after periods of rest.
Generally, prolonged exposure to high-pitched noise levels over a period of time can cause permanent damage. If this permanent damage occurs in the workplace, this can lead to a recordable incident that must be entered on the OSHA 300 Log.
To properly control and reduce workplace noise, you need to know the scope of the exposure. An industrial hygiene (IH) study can monitor a worker’s actual exposure over a work day so you know their time weighted average (TWA) exposure. The noise dosimetry and sound mapping completed in the IH study show how loud each area in your workplace is, where the noise is coming from, and how much of that noise is reaching your employee’s ears. This is reported as:
- A sound map with instant readings
- Noise dosimetry with time weighted averages – the sound level averaged over a continuous eight-hour period
- Noise dose – the percentage allowable of noise exposure to which a worker can be subject (a noise dose of 100% or more means that a worker has exceeded their daily limit for exposure)
Controlling Excessive Noise
Excessive noise and recordable hearing loss can be prevented by:
- Increasing the distance from noisy equipment
- Using quieter machines
- Isolating the noise source
- Installing acoustic panels
- Limiting worker exposure
- Using effective hearing protection
- Implementing a hearing conservation program
When choosing hearing protection, look for the label with a noise reduction rating (NRR). This indicates how well a pair of earplugs or earmuffs can reduce sound.
Note that one decibel in the NRR does not equate to one decibel of sound reduction. In laboratory conditions, the NRR does match the dB reduction, but we live in the real world where things are not perfect. To find the decibels of noise reduction, subtract seven from the NRR and then divide by two (i.e., (23 – 7) / 2 = 8). If your employees are exposed to 87 dB of noise and you use an earplug with an NRR of 23, this will reliably reduce their exposure to 79 dB.
Most hearing protection devices have an NRR of 15–35 dB. Higher NRR ratings are designed to protect workers with higher exposure to noise. The goal is to reduce noise exposure to a safe level without providing so much protection that workers struggle to communicate.
Annual Testing
When IH testing indicates the need for a hearing conservation program, the employer will need to test all of their workers and new hires to set a baseline audiogram. Annually thereafter, workers must have their hearing retested to compare to the baseline. The annual audiograms are compared to the baseline to see if there has been a standard threshold shift (STS) of 10 dB or more at 2000, 3000, and 4000 Hz in one or both ears.
If an employee’s hearing test (audiogram) reveals that the employee has experienced a work-related STS in hearing in one or both ears, this case will need to be recorded in an OSHA 300 Log. You can retest within 30 days of initial reported loss, but if consistent with an STS, it becomes recordable.
If your workplace has a hearing conservation program, it is important to continue monitoring changes in production, process, or controls. These changes could increase or decrease the number of employees who are required to be included in your hearing conservation program.
How Walden Can Help
Walden’s EHS staff can perform sound mapping, noise dosimetry, and audiometric testing. We can also write and implement a hearing conservation program and perform all required training for your team. If you need assistance, please contact EHS Director David Garner at 203-710-4376 or dgarner@walden-associates.com for further support.
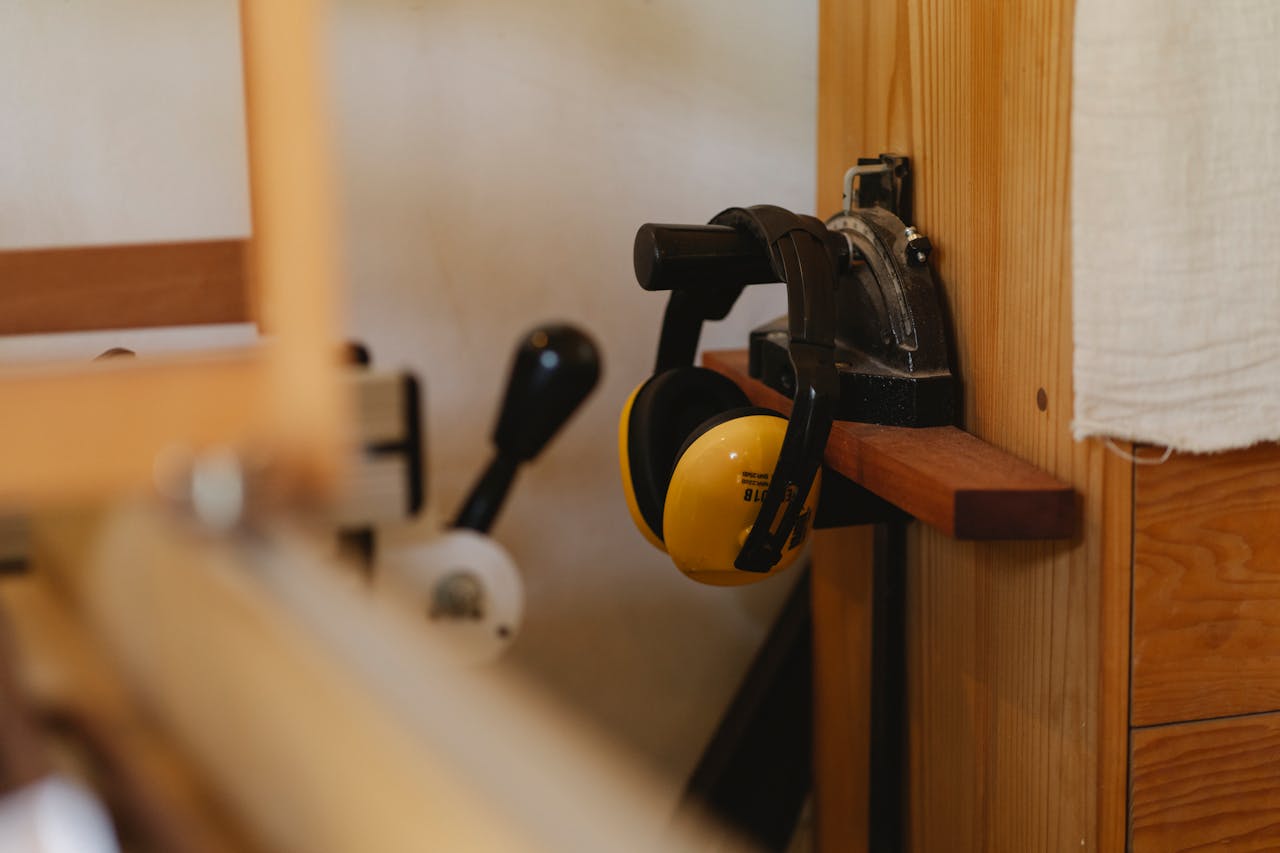
Work with Walden’s EHS team to develop a hearing conservation program! Contact us at 860-846-4069 to learn more about our services.