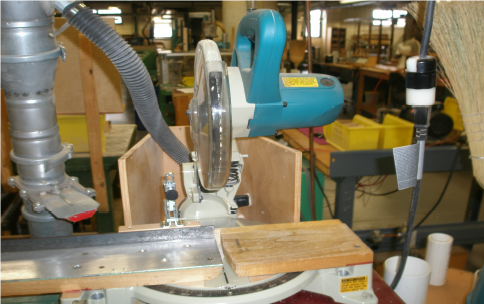
There are a few primary instances when manufacturers should test their air quality: upon setting up a new operation or piece of equipment, to identify the source of any potential exposures to hazardous material, and to confirm that operations all meet regulatory requirements. Both the substances of concern and the circumstances will determine the appropriate test to use.
TEST TO IDENTIFY YOUR ISSUE
In establishing controls, a consultant would first test the indoor air quality to confirm whether or not a company has an air quality issue. This baseline measurement also gives the designer some idea of the potential air quality issues so the appropriate engineering controls can be selected and designed. Once the system is in place, the company should retest the air quality to confirm that the control put in place is effective.
An indoor air quality test measures the chemical concentrations inside a facility where workers are exposed. The normal procedure is to place a small pump on the worker, with a tube that comes up to the collar near the breathing zone. A small opening takes in air and brings it through the pump into a cassette to collect contaminants in the air. That cassette is then tested to assess the concentration of certain emissions in the workplace, based on facility operations and chemical usage. In addition to personal testing, pumps would be placed in a few other general areas to measure the amount of chemicals in various areas of the workspace.
For concerns about an unidentified source—say, when a worker is reporting symptoms such as dizziness that the employer suspects is related to air quality—the consultant may use various meters to perform instantaneous, short- or long-term measurements. Meters can measure the amount of oxygen, carbon monoxide and certain other chemicals in the air.
TEST TO DEMONSTRATE COMPLIANCE
While certain air quality tests are used to identify a problem, other tests are required to confirm compliance with federal, state or local regulations on emission limits in the atmosphere. There are three testing methods that are typically used:
- The stack test, also referred to in USEPA regulations as a performance or source test, simply measures what’s leaving the building exhaust system. This may be required in order to demonstrate to the environmental agency that a facility is complying with the appropriate emission limits.
- A continuous emission monitor (CEM) continuously collects data on the amount of pollutants emitted into the atmosphere in exhaust gases from combustion or industrial processes. The CEM also records the data, as required by environmental agencies. A standard CEM system may consist of gas analyzers; gas sampling system; and temperature, flow and opacity monitors, all integrated with a data acquisition system. Typical monitored emissions include sulfur dioxide, nitrogen oxides, carbon monoxide, carbon dioxide, hydrogen chloride, airborne particulate matter and volatile organic compounds. CEM systems can also measure air flow, flue gas opacity and moisture.
- Technical requirements governing the use of CEMs are found in the U.S. Code of Federal Regulations’ Title 40: Protection of the Environment, 40 CFR Parts 60 and 75. State implementation plans are based on the USEPA’s regulatory authority, although some variation exists from state to state.
- Opacity Testing is a visual gauge of emissions from a stack to ensure that there is little to no smoke being emitted. Such testing is performed by a USEPA Method 9 Certified “Visible Emission Evaluator” who determines the opacity of the exhaust emitted.
Each of these test methods can be used together to determine that a facility is meeting emission limits.
TEST, DOCUMENT AND REPEAT
Testing is not to be done once and then forgotten. Depending on the regulatory requirements, testing may need to be repeated at a set frequency to confirm that the controls in place still work. Facility owners and employers also will need to maintain proof of this testing, and its success, as we’ll discuss in the next chapter.
Click here to download our full Air Quality Guide: Controlling the Air Quality in Your Facility: What You Need to Know About Your Regulatory Requirements and Options for Compliance.